PRODUCT DESIGN | SUPPLY CHAIN MANAGEMENT | SAAS
Facilitation of technology as medium
in manufacturing industry
Facilitation of technology as medium
in manufacturing industry
ROLE
Product Designer | System Designer
INTRODUCTION
The First Industrial Revolution erupted through the mechanisation of water and steam, second was driven by the use of electricity for mass production. The third was initiated by the disruption of computers and automation. The Fourth is what we are living in today which is transforming our surroundings from networking of systems, systems that we are part of on and behind the screens.
The First Industrial Revolution erupted through the mechanisation of water and steam, second was driven by the use of electricity for mass production. The third was initiated by the disruption of computers and automation. The Fourth is what we are living in today which is transforming our surroundings from networking of systems, systems that we are part of on and behind the screens.
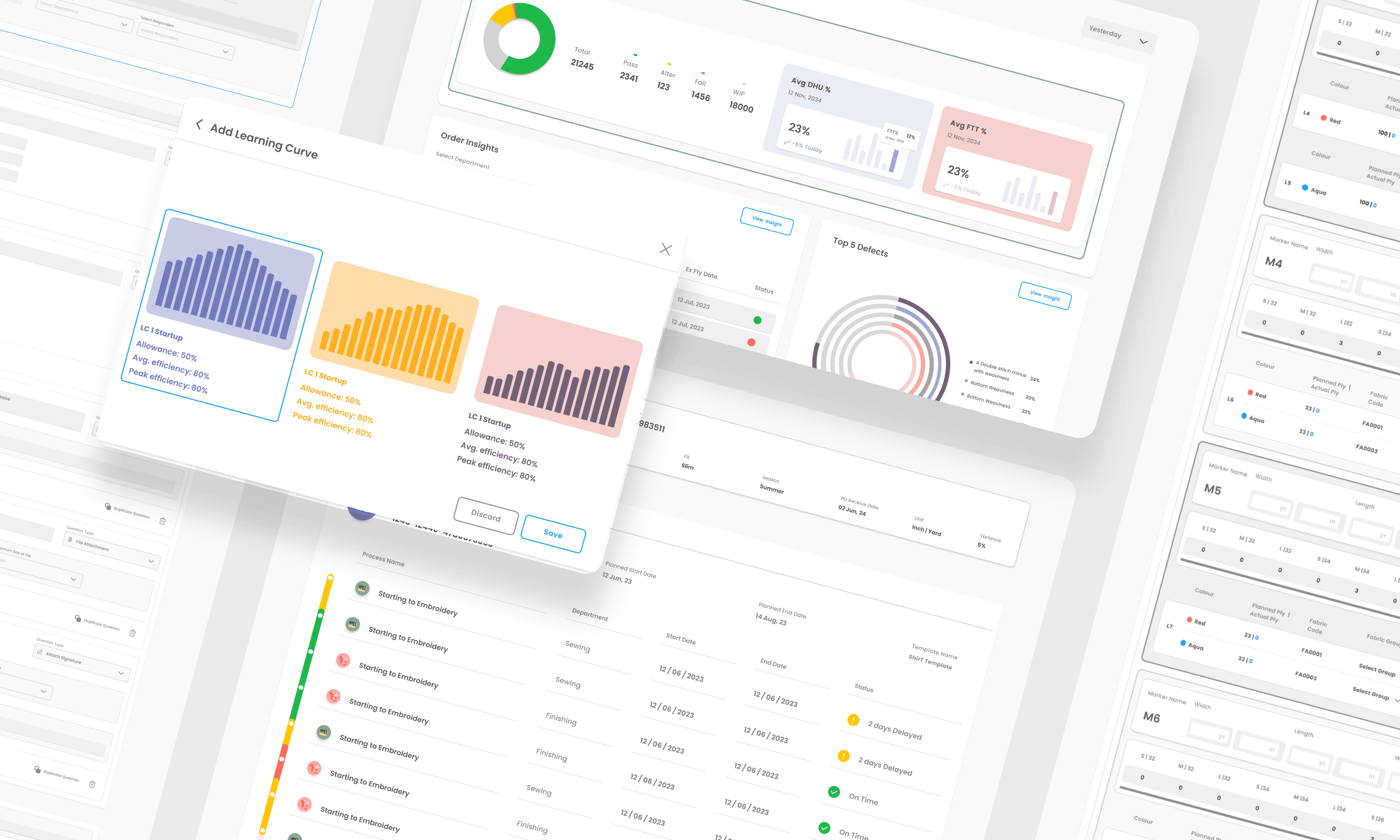
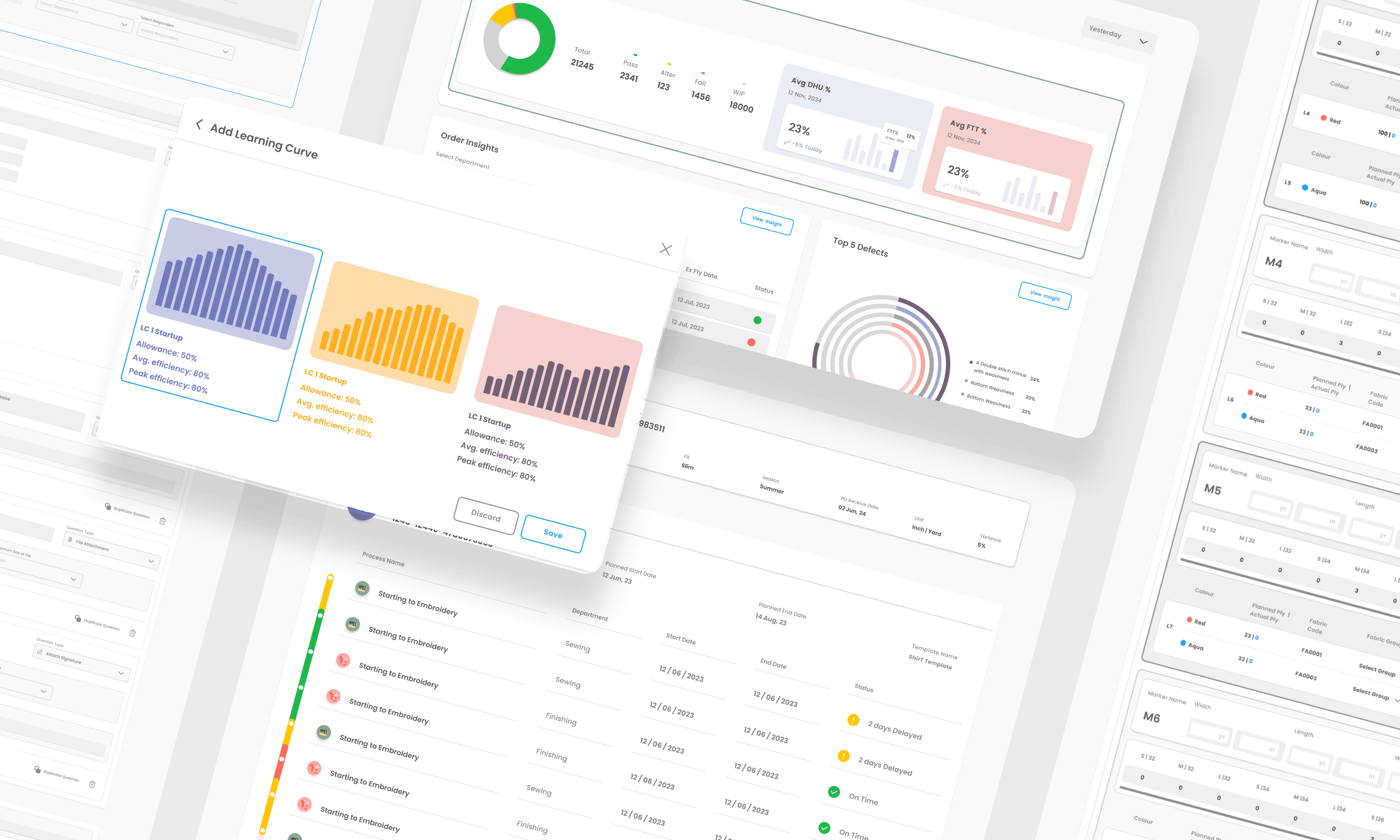
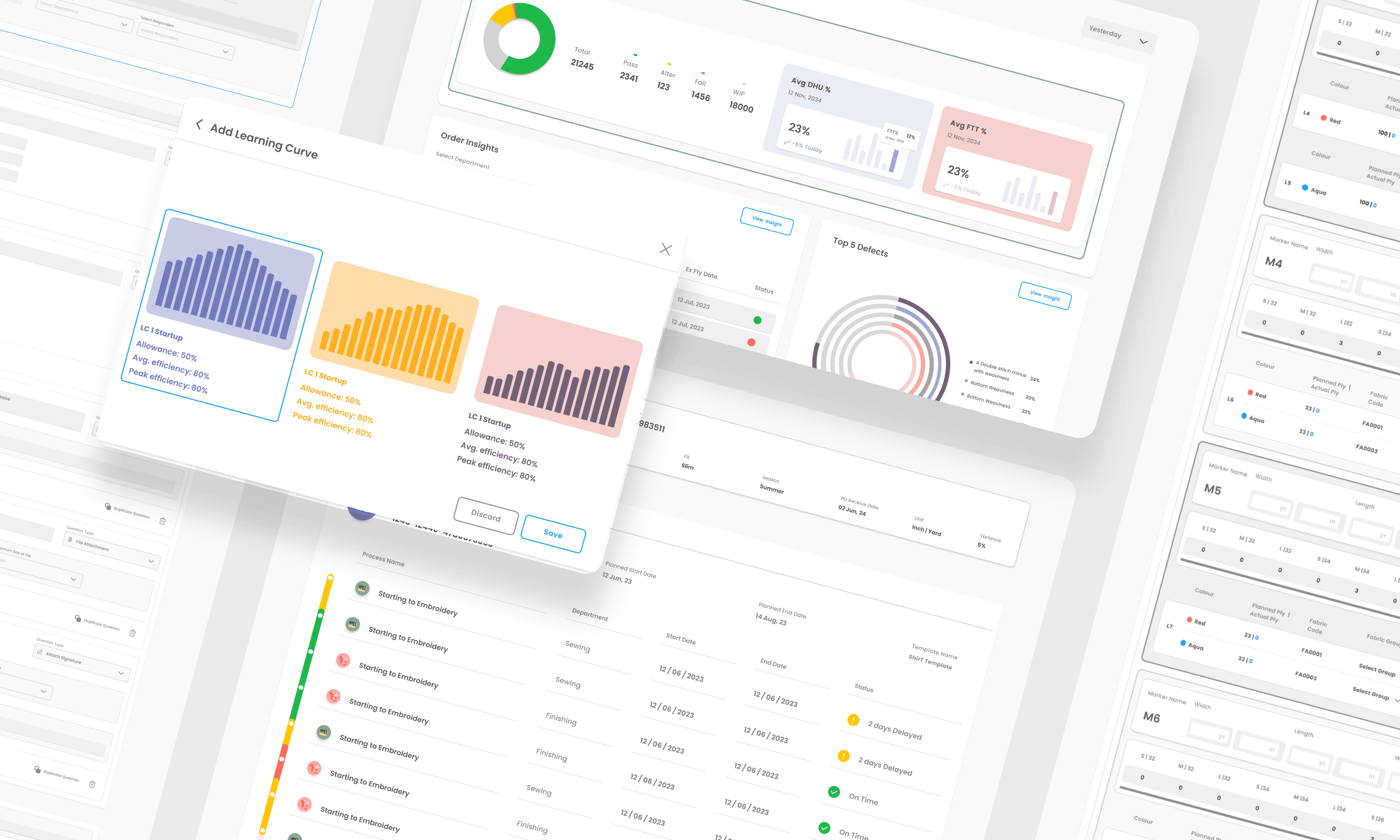
The integration of systems has profoundly impacted many front-facing systems that we use daily, enhancing both convenience and efficiency. However, some systems operate behind the scenes. With the intervention of technology, these systems can be transformed into experiences that reveal the underlying values associated with them. By connecting constituents across an end-to-end engagement, they create a cohesive and functional space within the broader ecosystem.
In the contemporary landscape of manufacturing industry, the facilitation of technology as system can revolutionise processes, ushering in an era of precision, efficiency, and adaptability. Working in a SaaS industry focused on manufacturing I understood need of the hour is a equitable, participative and an inclusive system that underlines and focus on the lack of a transition strategy and identification of relevant technologies required to achieve a cohesive participatory ecosystem.
Working with my team we encountered that there is a lack of clear bridge that connects the important checkpoints and milestones to relevant mediums of technology in manufacturing industry. SME’s have a keen interest in adapting and evolving as a automated smart manufacturing enterprises, but there are challenges on front including transparency, collaboration, communication and and an informed strategy for implementation as there is absence of appropriate technology tailored for specific floor requirements.
Manufacturing is a collaborative process which involves multiple stakeholders, there is a need of system which can provide visibility and identification of relevant and critical parameters that affect the processes and production and facilitates through an informed approach rather than an overhaul of technological ecosystem.
We created a system consisting five milestones when integrated together it provides an end-to-end engagement by creating a cohesive and functional ecosystem. These milestones as system are:
Plan: Streamline order management, optimise resource allocation, and enhance operational efficiency.
Inventory: Optimise inventory levels, ensure material availability, and reduce costs through effective tracking, analysis, and planning.
Curation: Maximise resource utilisation, minimise waste, and enhance overall production efficiency through optimised material usage and process management.
Production: Optimise production processes, enhance product quality, and increase overall efficiency through real-time monitoring, analysis, and improvement
Quality Check: Ensure product quality, efficiency in inspection processes, and data-driven improvement through robust quality control measures.
The integration of systems has profoundly impacted many front-facing systems that we use daily, enhancing both convenience and efficiency. However, some systems operate behind the scenes. With the intervention of technology, these systems can be transformed into experiences that reveal the underlying values associated with them. By connecting constituents across an end-to-end engagement, they create a cohesive and functional space within the broader ecosystem.
In the contemporary landscape of manufacturing industry, the facilitation of technology as system can revolutionise processes, ushering in an era of precision, efficiency, and adaptability. Working in a SaaS industry focused on manufacturing I understood need of the hour is a equitable, participative and an inclusive system that underlines and focus on the lack of a transition strategy and identification of relevant technologies required to achieve a cohesive participatory ecosystem.
Working with my team we encountered that there is a lack of clear bridge that connects the important checkpoints and milestones to relevant mediums of technology in manufacturing industry. SME’s have a keen interest in adapting and evolving as a automated smart manufacturing enterprises, but there are challenges on front including transparency, collaboration, communication and and an informed strategy for implementation as there is absence of appropriate technology tailored for specific floor requirements.
Manufacturing is a collaborative process which involves multiple stakeholders, there is a need of system which can provide visibility and identification of relevant and critical parameters that affect the processes and production and facilitates through an informed approach rather than an overhaul of technological ecosystem.
We created a system consisting five milestones when integrated together it provides an end-to-end engagement by creating a cohesive and functional ecosystem. These milestones as system are:
Plan: Streamline order management, optimise resource allocation, and enhance operational efficiency.
Inventory: Optimise inventory levels, ensure material availability, and reduce costs through effective tracking, analysis, and planning.
Curation: Maximise resource utilisation, minimise waste, and enhance overall production efficiency through optimised material usage and process management.
Production: Optimise production processes, enhance product quality, and increase overall efficiency through real-time monitoring, analysis, and improvement
Quality Check: Ensure product quality, efficiency in inspection processes, and data-driven improvement through robust quality control measures.
PLAN
PLAN
Key Features:
Simultaneous Order Mapping: Enable factory owners to efficiently manage multiple orders across different outlets simultaneously.
Capacity Prediction: Utilize data-driven insights to forecast resource utilization and optimize production planning.
Transparency and Control: Implement robust reporting and authorization mechanisms for enhanced visibility and governance.
Key Features:
Simultaneous Order Mapping: Enable factory owners to efficiently manage multiple orders across different outlets simultaneously.
Capacity Prediction: Utilize data-driven insights to forecast resource utilization and optimize production planning.
Transparency and Control: Implement robust reporting and authorization mechanisms for enhanced visibility and governance.
Key Features:
Simultaneous Order Mapping: Enable factory owners to efficiently manage multiple orders across different outlets simultaneously.
Capacity Prediction: Utilize data-driven insights to forecast resource utilization and optimize production planning.
Transparency and Control: Implement robust reporting and authorization mechanisms for enhanced visibility and governance.
Key Features:
Simultaneous Order Mapping: Enable factory owners to efficiently manage multiple orders across different outlets simultaneously.
Capacity Prediction: Utilize data-driven insights to forecast resource utilization and optimize production planning.
Transparency and Control: Implement robust reporting and authorization mechanisms for enhanced visibility and governance.
INVENTORY
Key Features:
Material and Equipment Usage Tracking: Monitor consumption patterns of materials and equipment to identify usage trends and anomalies.
Inspection and Maintenance: Schedule and track inspections of materials and equipment to maintain quality and prevent breakdowns.
Predictive Inventory: Forecast material requirements based on production plans, historical data, and demand patterns.
Supplier Management: Maintain a comprehensive directory of suppliers, including contact information, pricing, and performance metrics.
Key Features:
Material and Equipment Usage Tracking: Monitor consumption patterns of materials and equipment to identify usage trends and anomalies.
Inspection and Maintenance: Schedule and track inspections of materials and equipment to maintain quality and prevent breakdowns.
Predictive Inventory: Forecast material requirements based on production plans, historical data, and demand patterns.
Supplier Management: Maintain a comprehensive directory of suppliers, including contact information, pricing, and performance metrics.
Key Features:
Material and Equipment Usage Tracking: Monitor consumption patterns of materials and equipment to identify usage trends and anomalies.
Inspection and Maintenance: Schedule and track inspections of materials and equipment to maintain quality and prevent breakdowns.
Predictive Inventory: Forecast material requirements based on production plans, historical data, and demand patterns.
Supplier Management: Maintain a comprehensive directory of suppliers, including contact information, pricing, and performance metrics.
CURATION
Key Features:
Optimized Material Allocation: Determine the most efficient use of materials for each product or order, considering factors such as quantity, quality, and cost.
Efficiency Enhancement: Identify and implement process improvements to reduce production time, labor costs, and material waste.
WIP Tracking: Monitor work-in-progress (WIP) inventory to optimize production flow and identify bottlenecks.
Waste Reduction: Implement strategies to minimize waste in all forms, including material, labor, and energy.
Key Features:
Optimized Material Allocation: Determine the most efficient use of materials for each product or order, considering factors such as quantity, quality, and cost.
Efficiency Enhancement: Identify and implement process improvements to reduce production time, labor costs, and material waste.
WIP Tracking: Monitor work-in-progress (WIP) inventory to optimize production flow and identify bottlenecks.
Waste Reduction: Implement strategies to minimize waste in all forms, including material, labor, and energy.
Key Features:
Optimized Material Allocation: Determine the most efficient use of materials for each product or order, considering factors such as quantity, quality, and cost.
Efficiency Enhancement: Identify and implement process improvements to reduce production time, labor costs, and material waste.
WIP Tracking: Monitor work-in-progress (WIP) inventory to optimize production flow and identify bottlenecks.
Waste Reduction: Implement strategies to minimize waste in all forms, including material, labor, and energy.
PRODUCTION
Key Features:
End-to-End Product Tracking: Monitor product movement through the production process to ensure timely completion and accurate inventory management.
Labor and Manufacturing Efficiency: Analyze labor performance and production metrics to identify bottlenecks and optimize resource allocation.
Real-Time Error Detection: Implement a live feedback system to detect and address production errors promptly, minimizing defects and rework.
Quality Assurance: Integrate quality control checkpoints throughout the production process to ensure product conformance to standards.
Key Features:
End-to-End Product Tracking: Monitor product movement through the production process to ensure timely completion and accurate inventory management.
Labor and Manufacturing Efficiency: Analyze labor performance and production metrics to identify bottlenecks and optimize resource allocation.
Real-Time Error Detection: Implement a live feedback system to detect and address production errors promptly, minimizing defects and rework.
Quality Assurance: Integrate quality control checkpoints throughout the production process to ensure product conformance to standards.
Key Features:
End-to-End Product Tracking: Monitor product movement through the production process to ensure timely completion and accurate inventory management.
Labor and Manufacturing Efficiency: Analyze labor performance and production metrics to identify bottlenecks and optimize resource allocation.
Real-Time Error Detection: Implement a live feedback system to detect and address production errors promptly, minimizing defects and rework.
Quality Assurance: Integrate quality control checkpoints throughout the production process to ensure product conformance to standards.
Key Features:
End-to-End Product Tracking: Monitor product movement through the production process to ensure timely completion and accurate inventory management.
Labor and Manufacturing Efficiency: Analyze labor performance and production metrics to identify bottlenecks and optimize resource allocation.
Real-Time Error Detection: Implement a live feedback system to detect and address production errors promptly, minimizing defects and rework.
Quality Assurance: Integrate quality control checkpoints throughout the production process to ensure product conformance to standards.
QUALITY CHECK
Key Features:
Efficient Quality Checking: Streamline inspection processes to reduce inspection time and improve accuracy.
Audit Tracking: Maintain a comprehensive record of quality audits to monitor performance and identify trends.
Labor Optimisation: Allocate inspection resources effectively to maximise labor utilisation.
Defect Analysis: Analyse defect data to identify root causes and implement corrective actions.
Key Features:
Efficient Quality Checking: Streamline inspection processes to reduce inspection time and improve accuracy.
Audit Tracking: Maintain a comprehensive record of quality audits to monitor performance and identify trends.
Labor Optimisation: Allocate inspection resources effectively to maximise labor utilisation.
Defect Analysis: Analyse defect data to identify root causes and implement corrective actions.
VISION
Manufacturing technologies have enormous potential to change the manufacturing landscape for small and large manufacturers alike. There is lack of decision making tools that cater the gap of communication and integration associated these technologies benefitting the stakeholders with cost, labour and efficiency.
The above explained modules are curated as an ecosystem that integrates with each other and make sense with and without the dependability of the software in a way that technology as a medium facilitates automation with informed input of multiple stake holders and their needs for enhancing both convenience and efficiency.